CRK Service Design
Processes: Research, Needfinding, User-Centered Design, Rapid Prototyping, Fabrication and Manufacturing, Engineering Analysis, and FEAIndividual Contributions:
- Research: Literature review, stakeholder analysis, interviews, design criteria
- Prototyping: Sketching, low fidelity, user testing
- Engineering: 3D models, Engineering analysis, FEA
- Deliverables: Assembly, installation, fabrication package for client, educational model
Below is a summary with only my individual contributions. To see the entire project, click here.

The Problem: Chattahoochee River Keeper, an Atlanta non-profit, wished to improve their Blandalong plastics trap in terms of capacity, effectiveness, and servicibility.
The Result: Researched, designed, and fabricated a system of walled grates that improved the trap’s capacity by 150%. The walls also separate organic matter and increase the speed at which the trash can be gathered. A manufacturing and repair plan was provided for easy servicing, repair, and replication for other trash traps. Additionally, a scale model of the plastic trap was created to aid CRK with their outreach program.
Research
What is the environment like?

Insight: Proctor Creek has already been extensively studied and existing traps are in the optimal to maximize impact.
What are the affected parties?
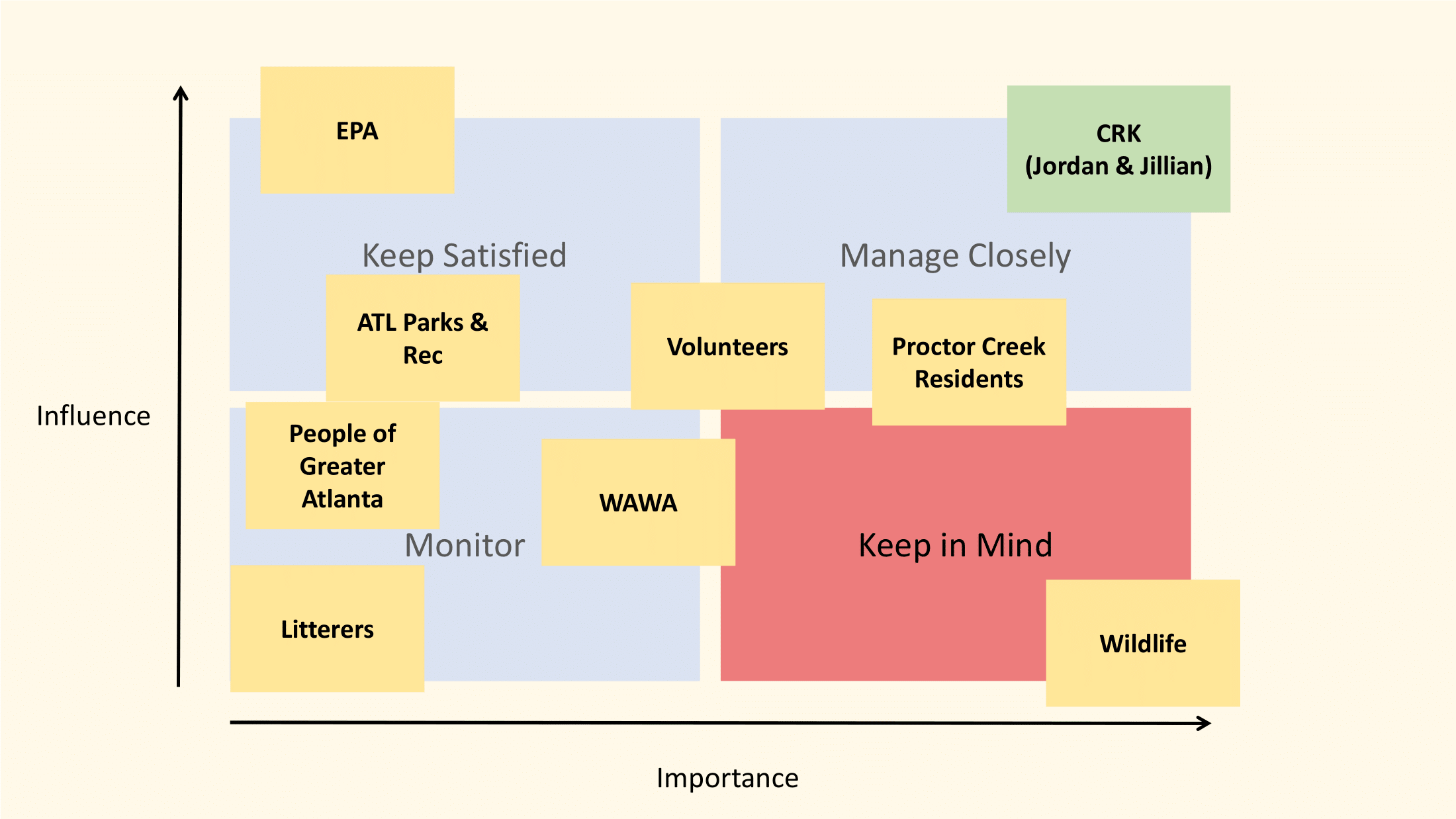

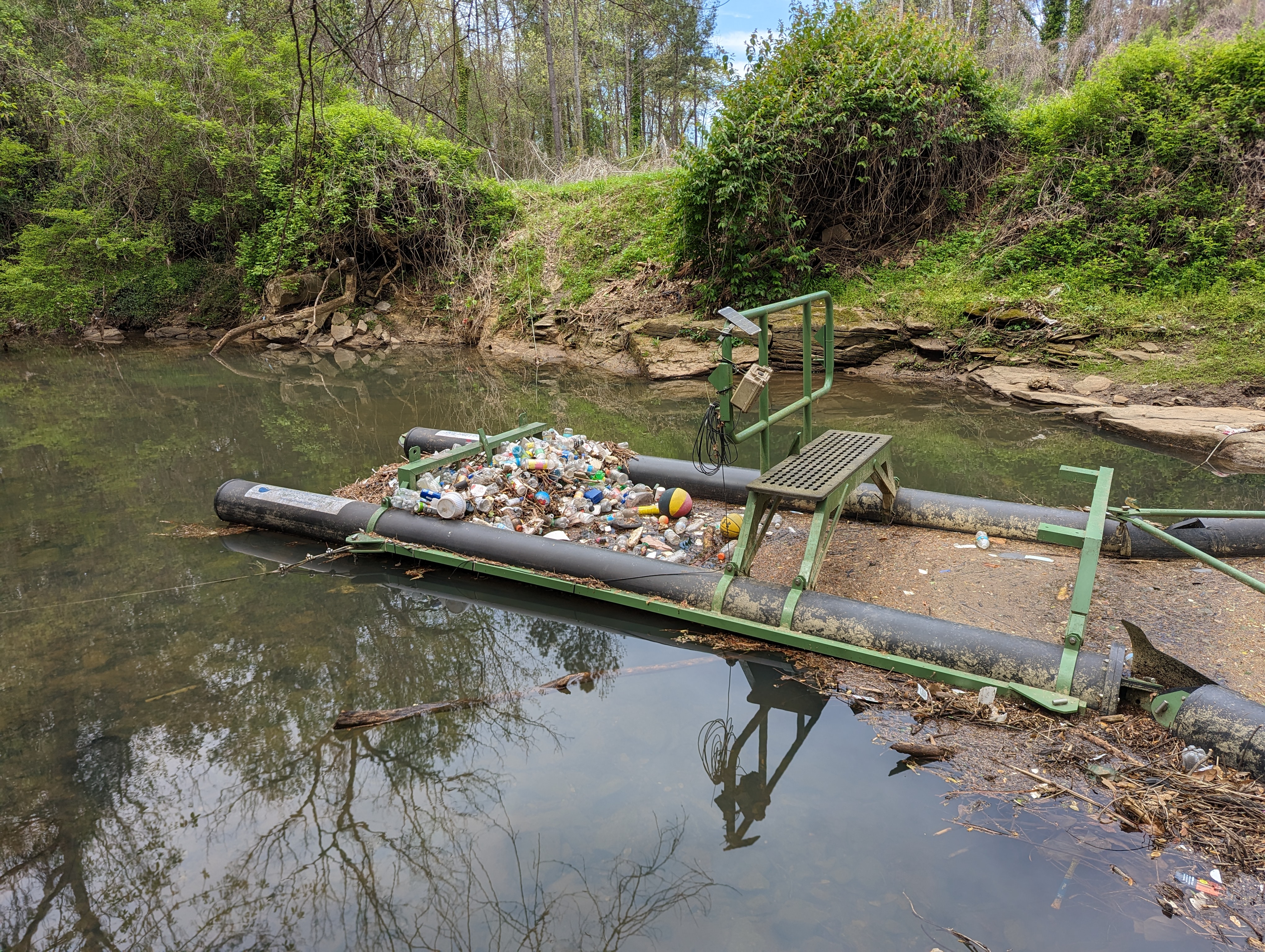
1st Round of Prototyping
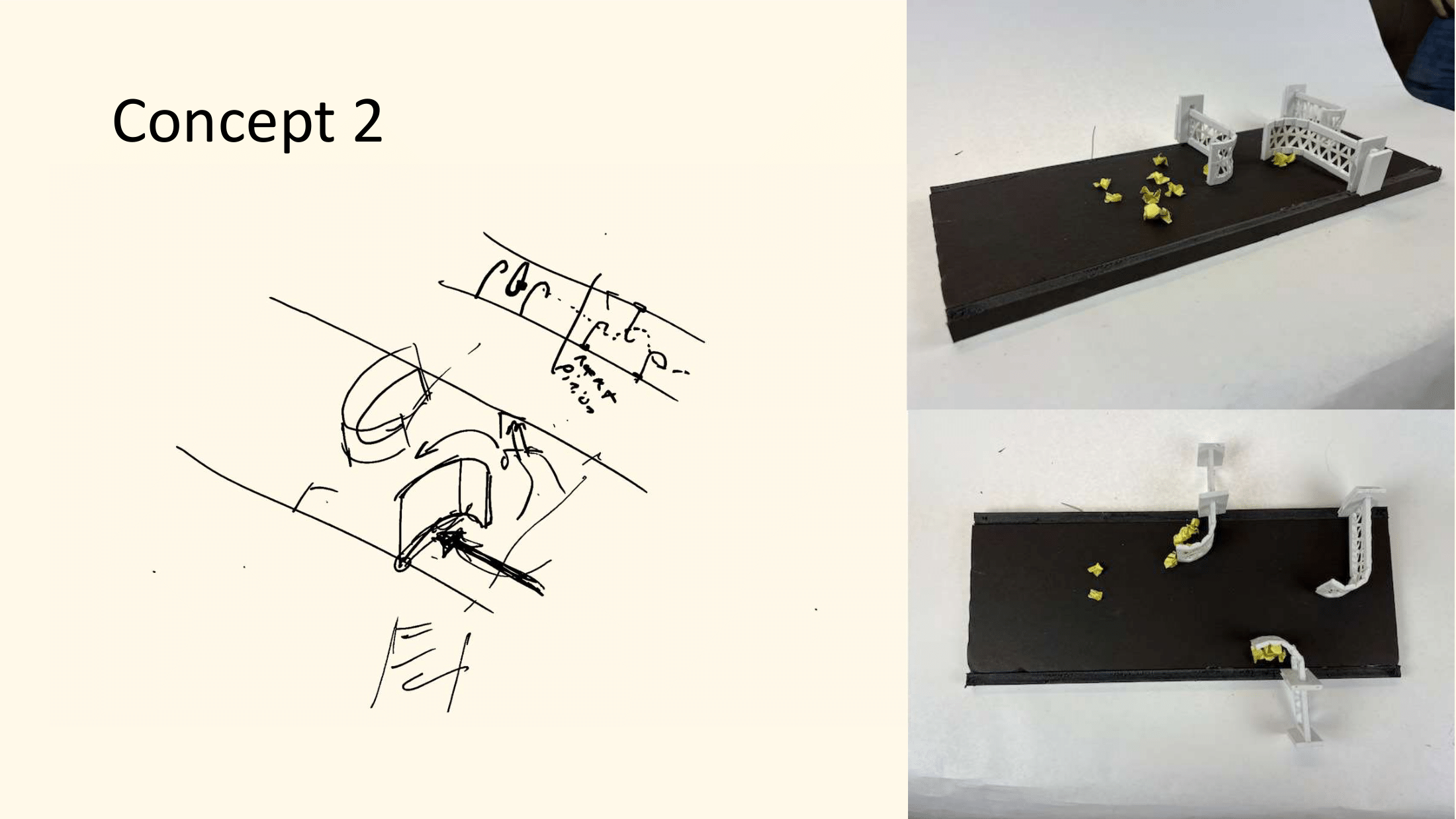
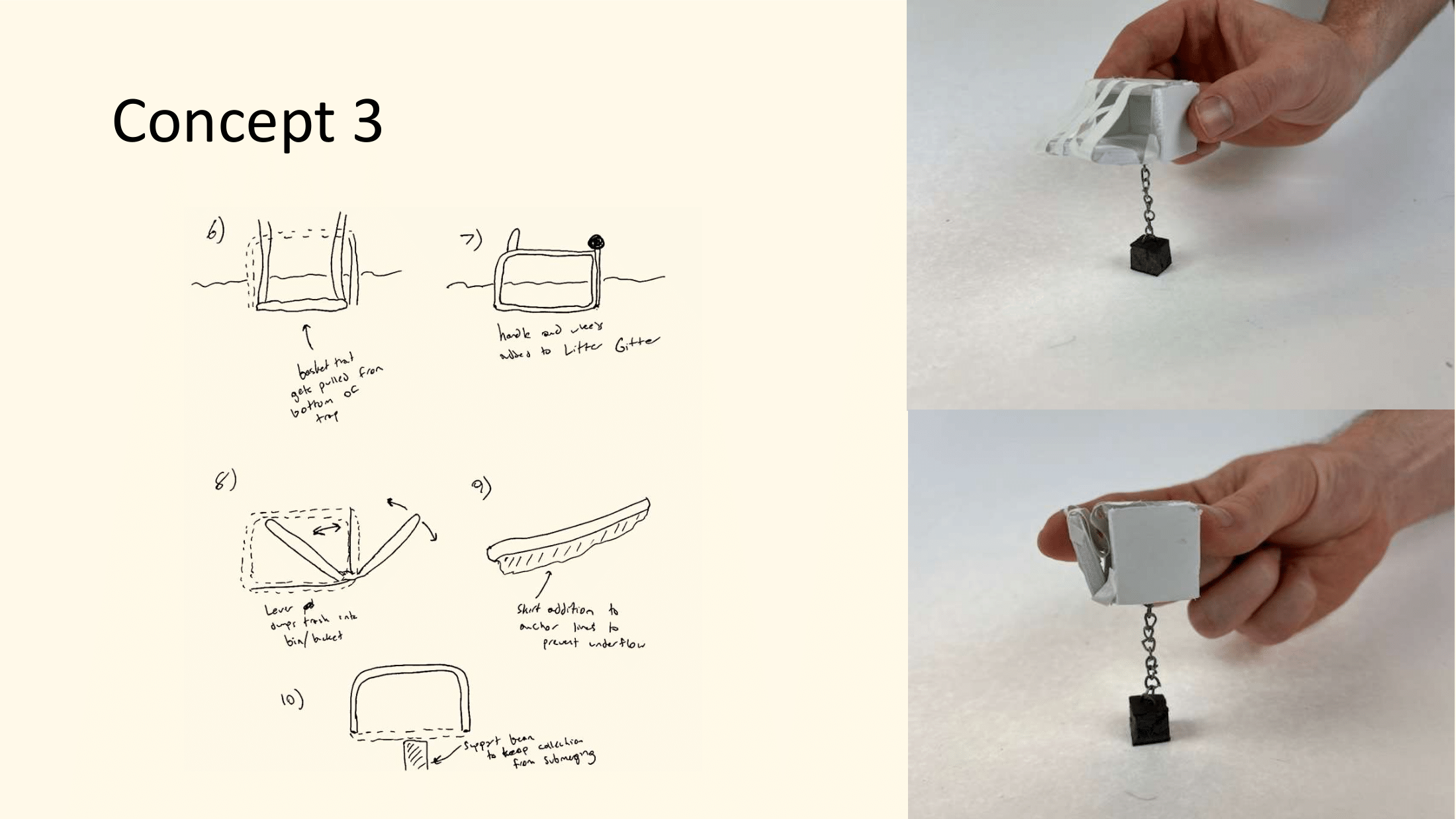
The feedback was:
-
Focus more on increasing capacity and minimize trash loss of the traps
- Smaller traps are more difficult to service because of their limited access from the top.
- There aren’t enough resources to effectively service additional traps.
- CRK would like an easier way to access the larger traps – they currently climb over the top while servicing.
- It’s a lot easier to sort the trash while still in the water instead of doing it on land.
- Try to avoid large objects (logs, trees, etc.) from getting into the trap.
2nd Round of Prototyping

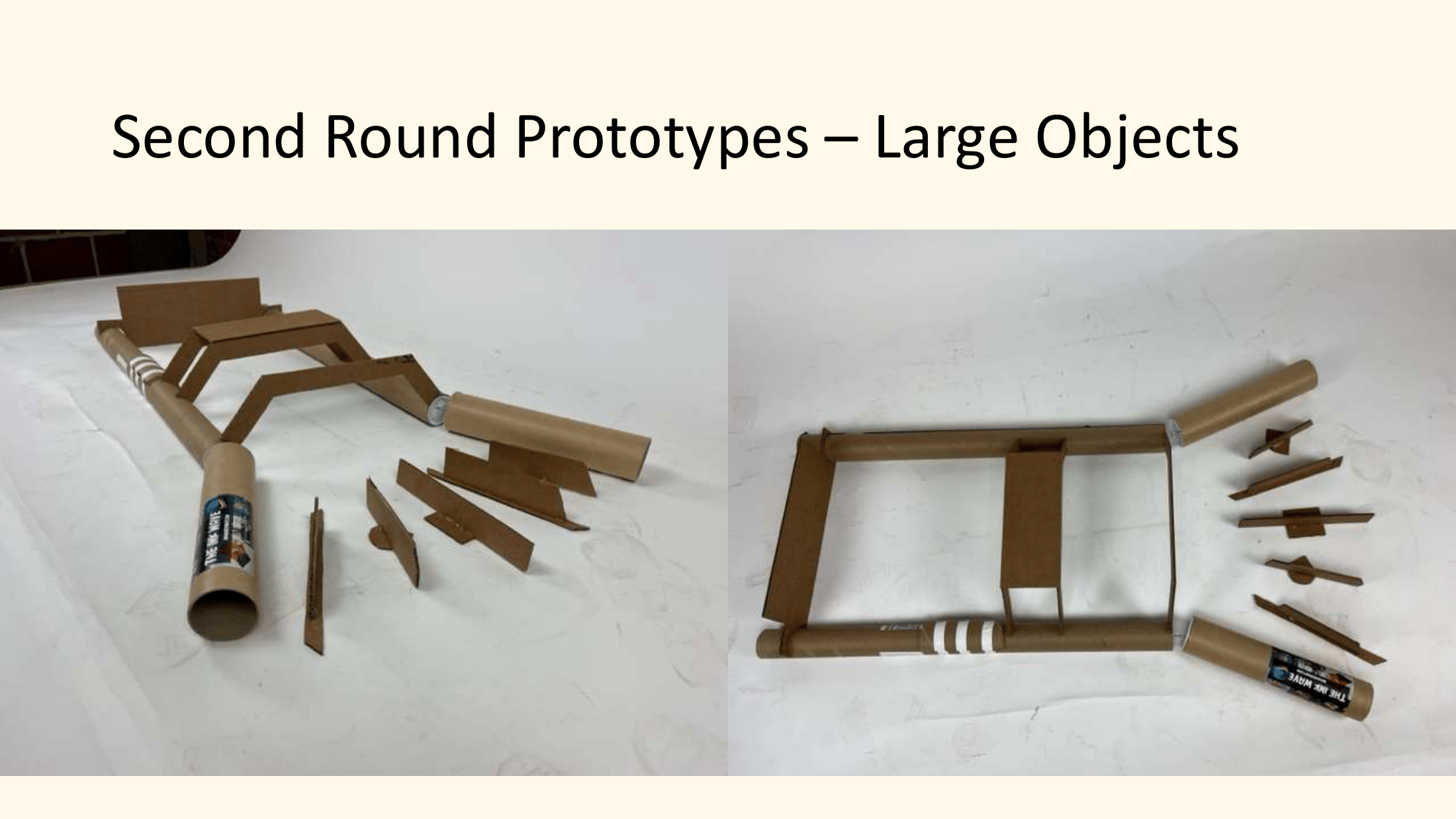
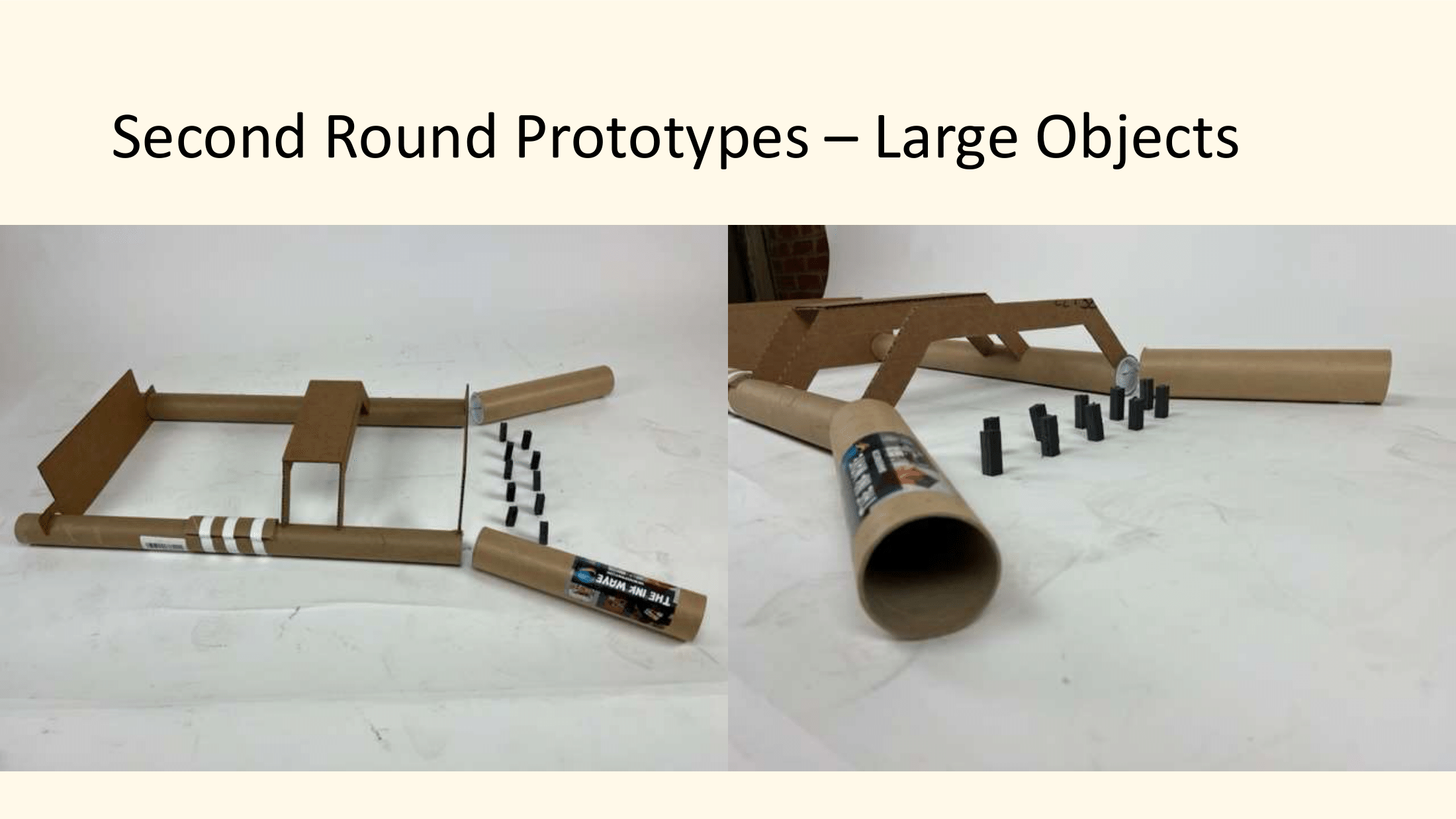
The feedback was:
Prevent Trash Loss / Trap Capcity
-
Maximize height at back of trap
- Sliding wall is first pick
- Would like if part that slides out is able to sift trash
- Hinges and slots are susceptible to getting jammed with trash
- Need method to clean
Prevent Large Debris Jams
- Logs sit much lower in the water than the trash
- Trap needs to be self contained
- Could funnel logs somewhere
- Fin form factor suits log travel path
- Large Log: 18” – 24” dia, 20 ft long
- Branch: 2" -4” dia, 10 ft long
Insight: The prevention of large debris jams was determined to be outside of the scope of the projects due to the cost and time associated with making the system self contained.
Environmental Constraints
![]()
CRK preferred the sliding mechanism for the walls. Iterations of how to attach the walls to the rails.
Both Jordan and Gillian liked the slid-in rail method (left) the most as it was the simplest to use and clean while still being secure.
I ran some structural analyses in Solidworks to verify whether the final design would withstand the expected known environmental conditions.
The maximum simulated rail deformation was 9mm with a max stress of 200MPa. Both of these values are significantly below the point of failure.
The maximum simulated rail deformation was 1.8mm with a max stress of 20MPa. Both of these values are significantly below the point of failure.
To approximate the efficiency of our trap capture system we took measurements of the volume of trash that would overflow from the trap during storm surges.
![]()
This data is captured by USGS (resource mentioned earlier) during a week of heavy rains while we worked on the project. The three peak creek flow rates are shown and averaged together.
![]()
We found 24 occurrences over the last year where the flow rate of Proctor Creek went over 500ft³/s. This velocity correlates to sudden changes in creek height. In these 24 occurrences, there were 186 15 min periods where the flow rate was above this threshold.
![Walls used to clean trash in Proctor Creek]()
![Walls used to clean trash in Proctor Creek]()
![1. Cutting slots in the hard plastic skirt]()
![2. Bolting clips on clips and then riveting rails to the clips]()
![3. Inserting the walls into the rails and testing for fit]()
![4. Finishing touches and view of the installed system from the top]()
All Solidworks and STL files were provided.
Set up of the educational model. The model consists of a tank with two sections that are seperated by an acrylic sheet. The bottom contains a water pump that simulates the creek flow. On top of the acryllic sheet, the 3d printed model floats and cut up sponges represent the trash.
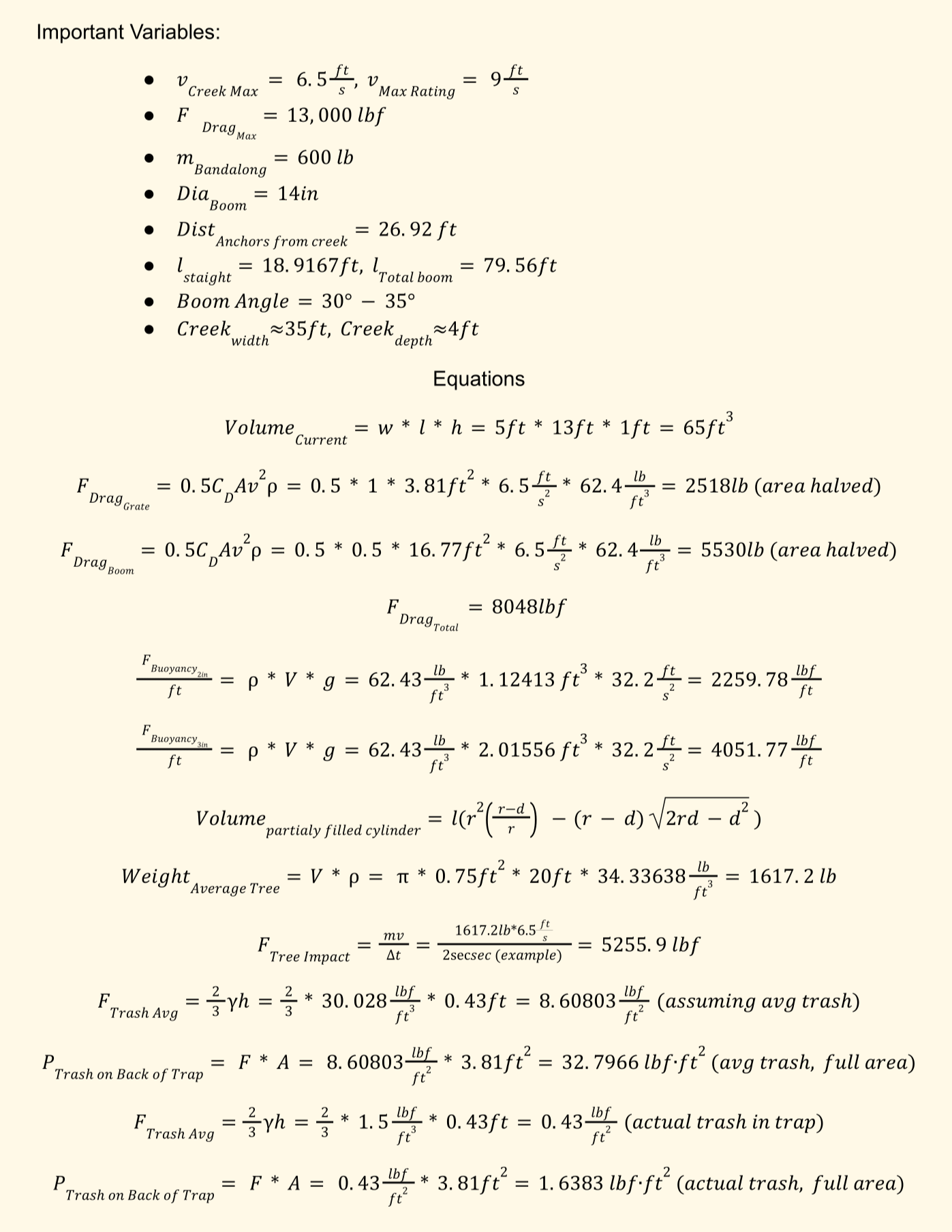
Final Design Verification
CRK preferred the sliding mechanism for the walls. Iterations of how to attach the walls to the rails.

Both Jordan and Gillian liked the slid-in rail method (left) the most as it was the simplest to use and clean while still being secure.
I ran some structural analyses in Solidworks to verify whether the final design would withstand the expected known environmental conditions.
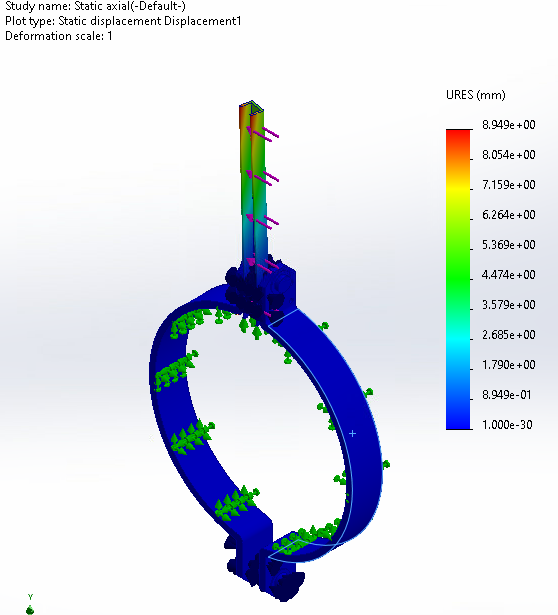
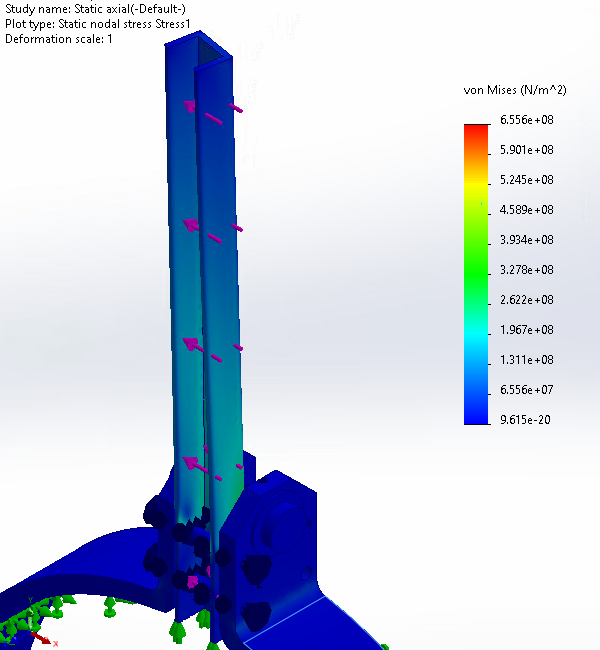
The maximum simulated rail deformation was 9mm with a max stress of 200MPa. Both of these values are significantly below the point of failure.
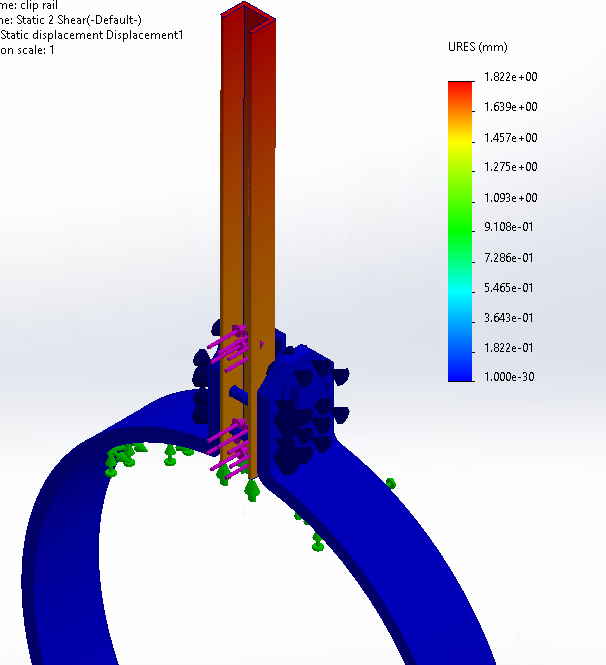
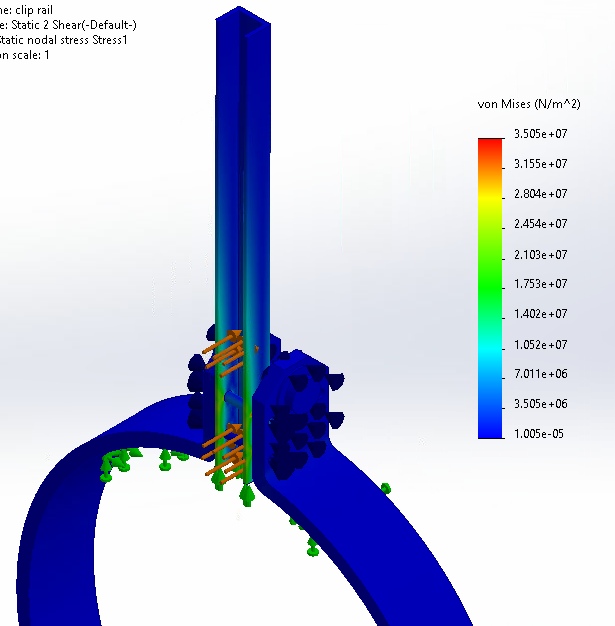
The maximum simulated rail deformation was 1.8mm with a max stress of 20MPa. Both of these values are significantly below the point of failure.
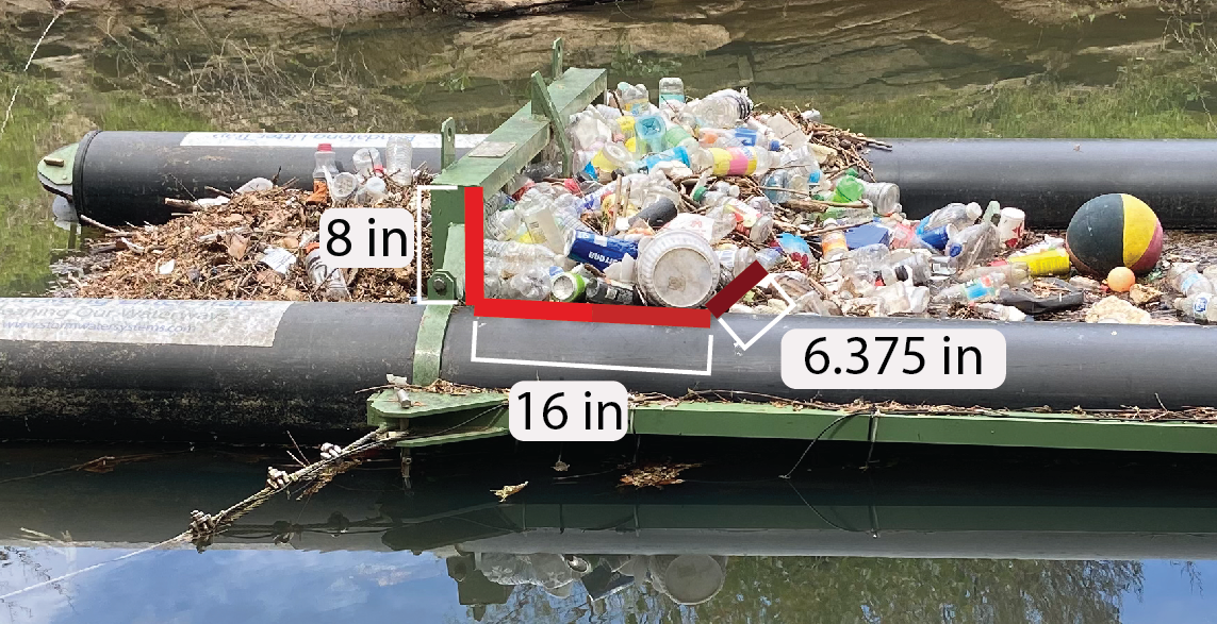
To approximate the efficiency of our trap capture system we took measurements of the volume of trash that would overflow from the trap during storm surges.

This data is captured by USGS (resource mentioned earlier) during a week of heavy rains while we worked on the project. The three peak creek flow rates are shown and averaged together.
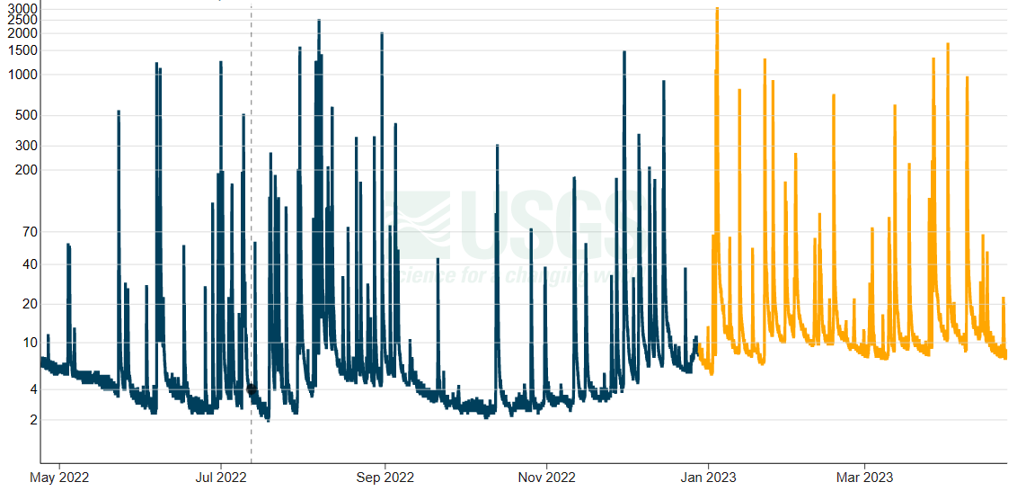
We found 24 occurrences over the last year where the flow rate of Proctor Creek went over 500ft³/s. This velocity correlates to sudden changes in creek height. In these 24 occurrences, there were 186 15 min periods where the flow rate was above this threshold.
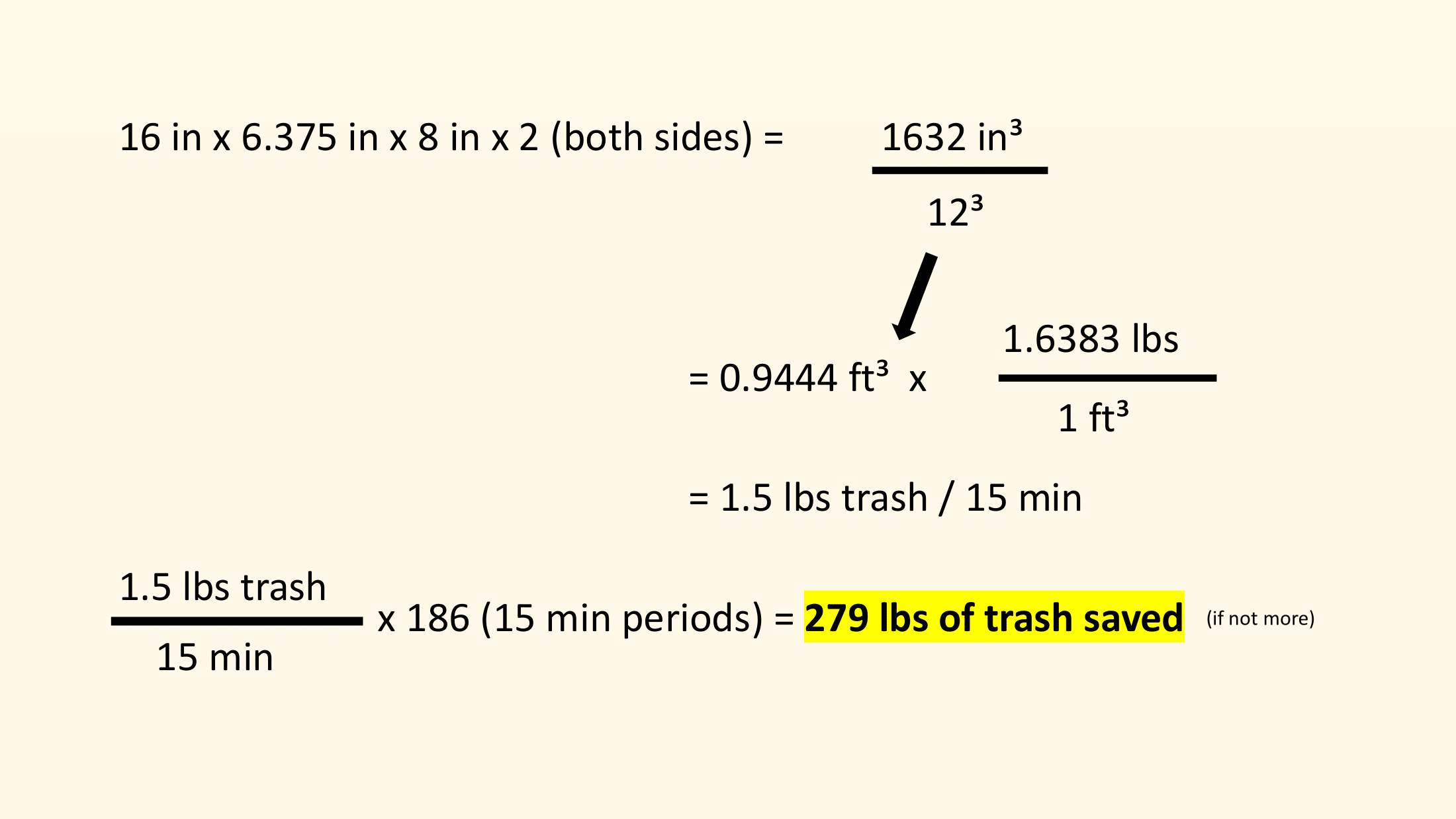
Final Design Fabrication: Walls
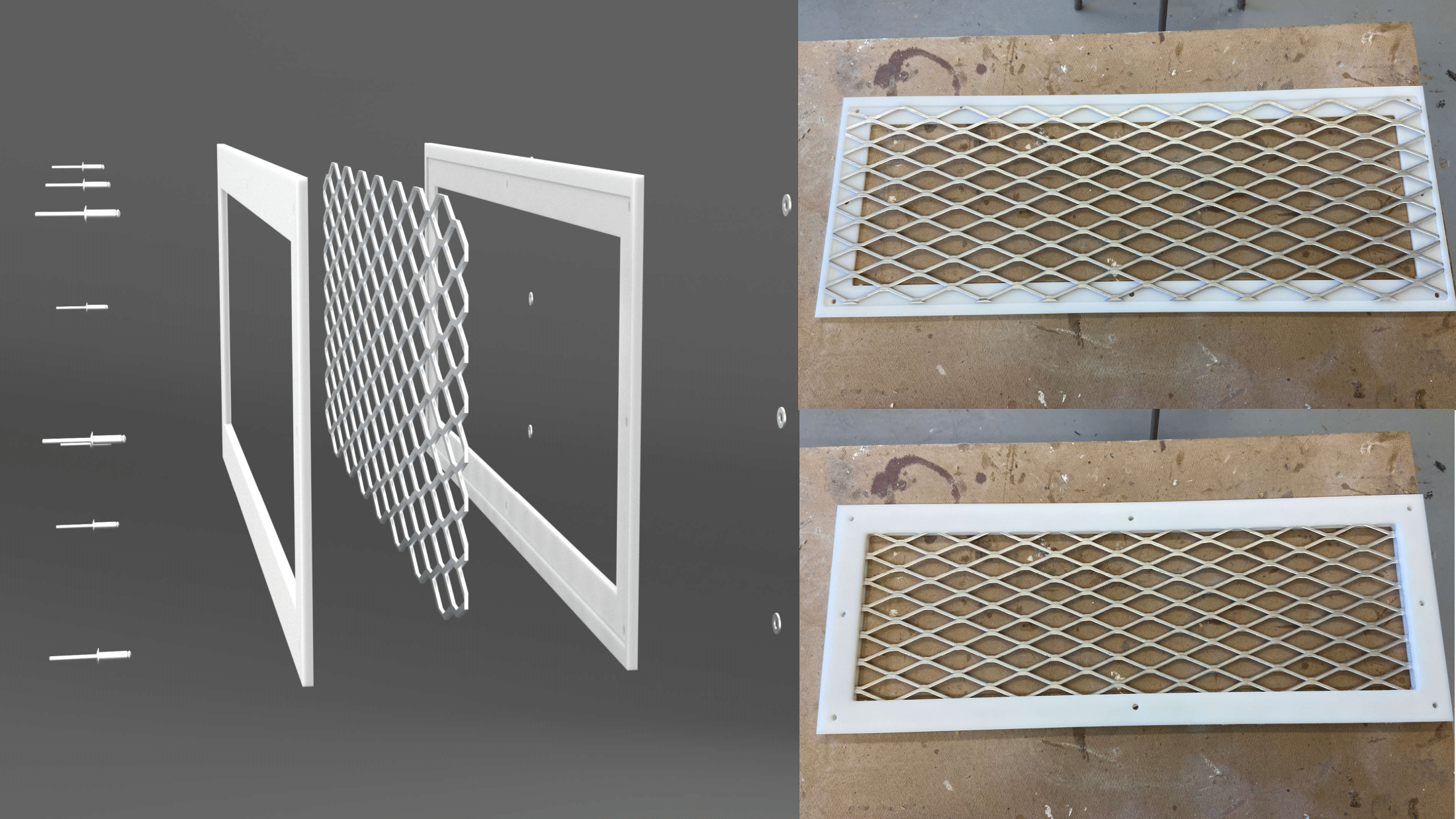

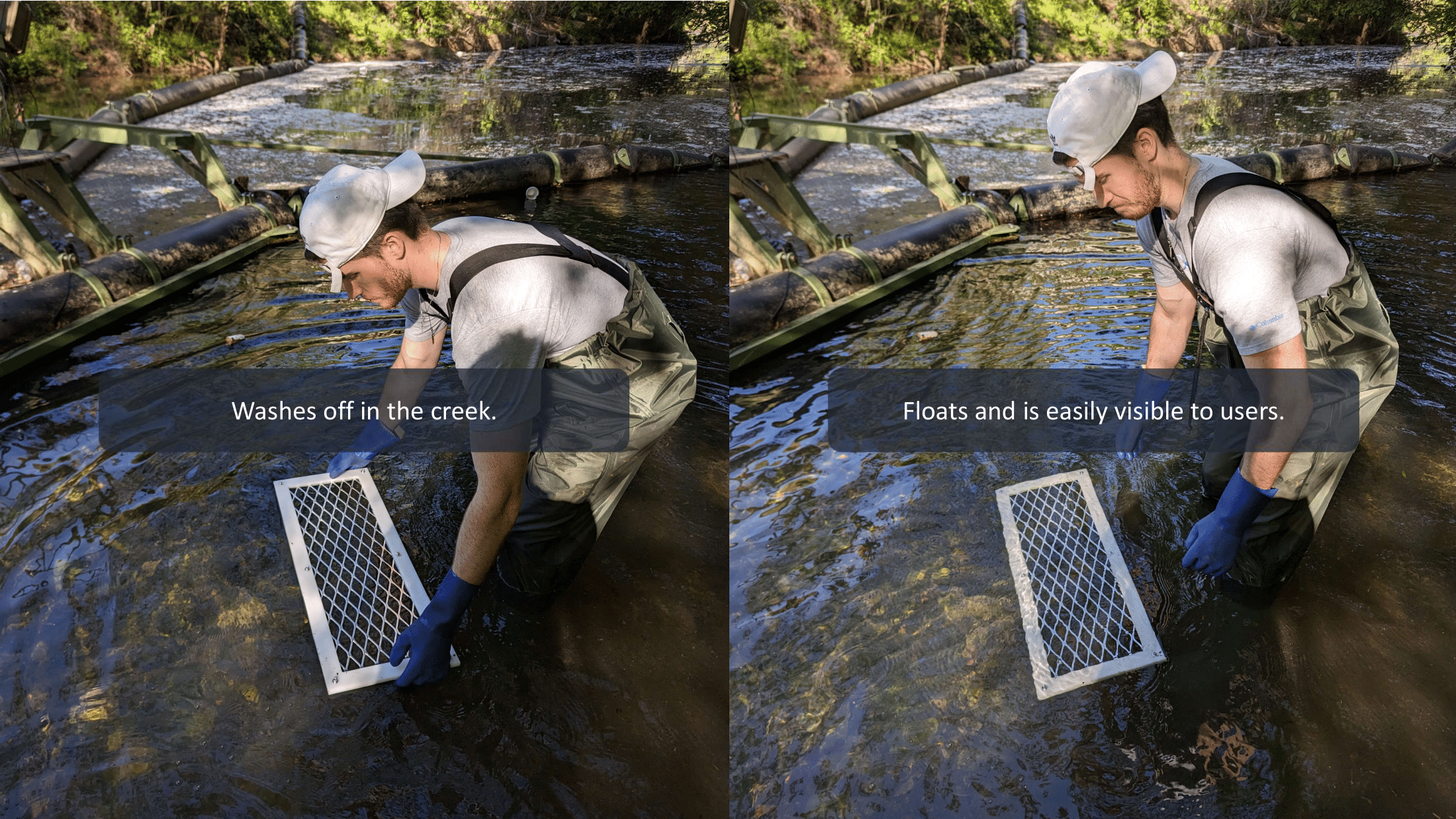
Final Design Fabrication: Installation
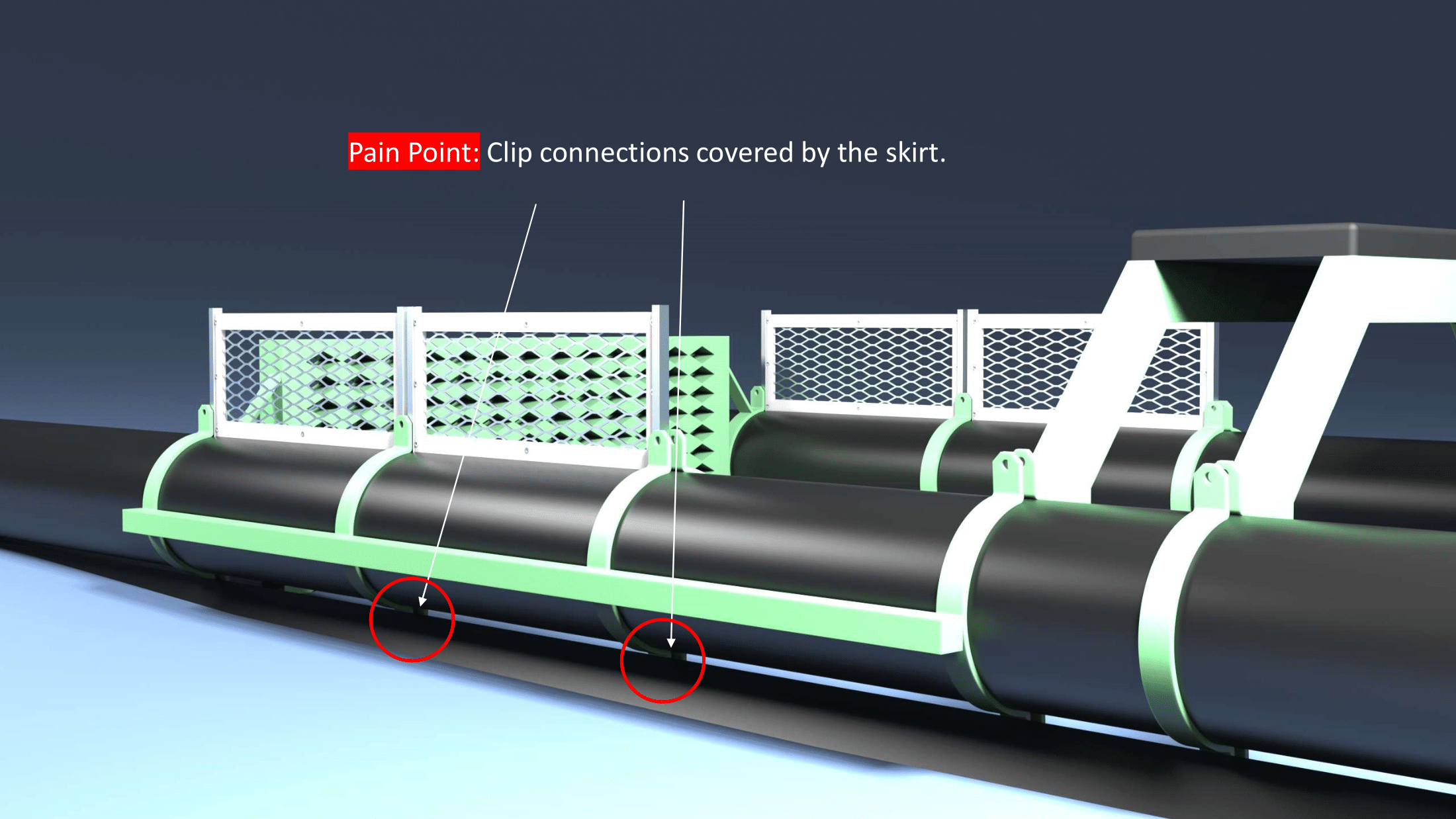

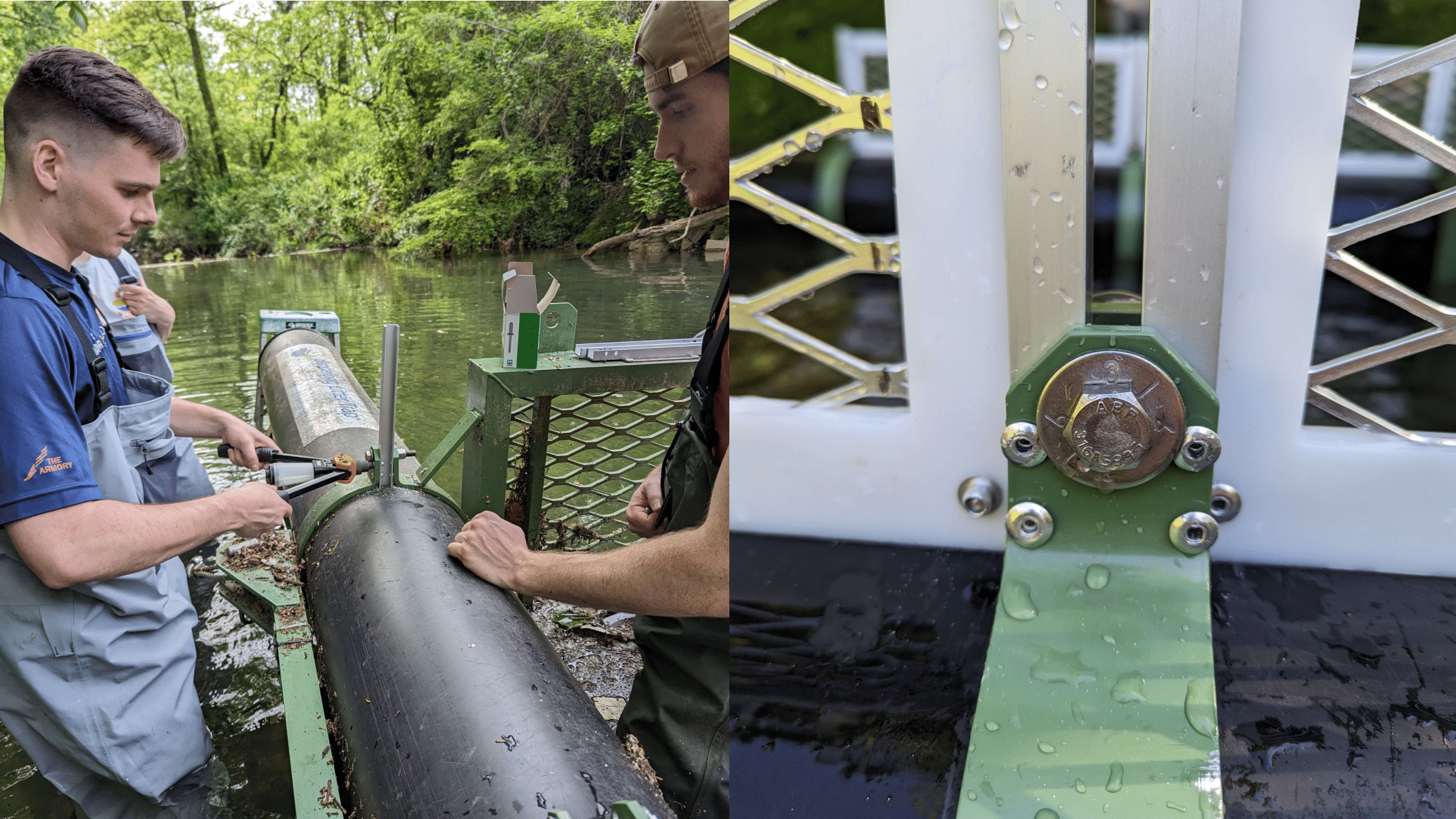
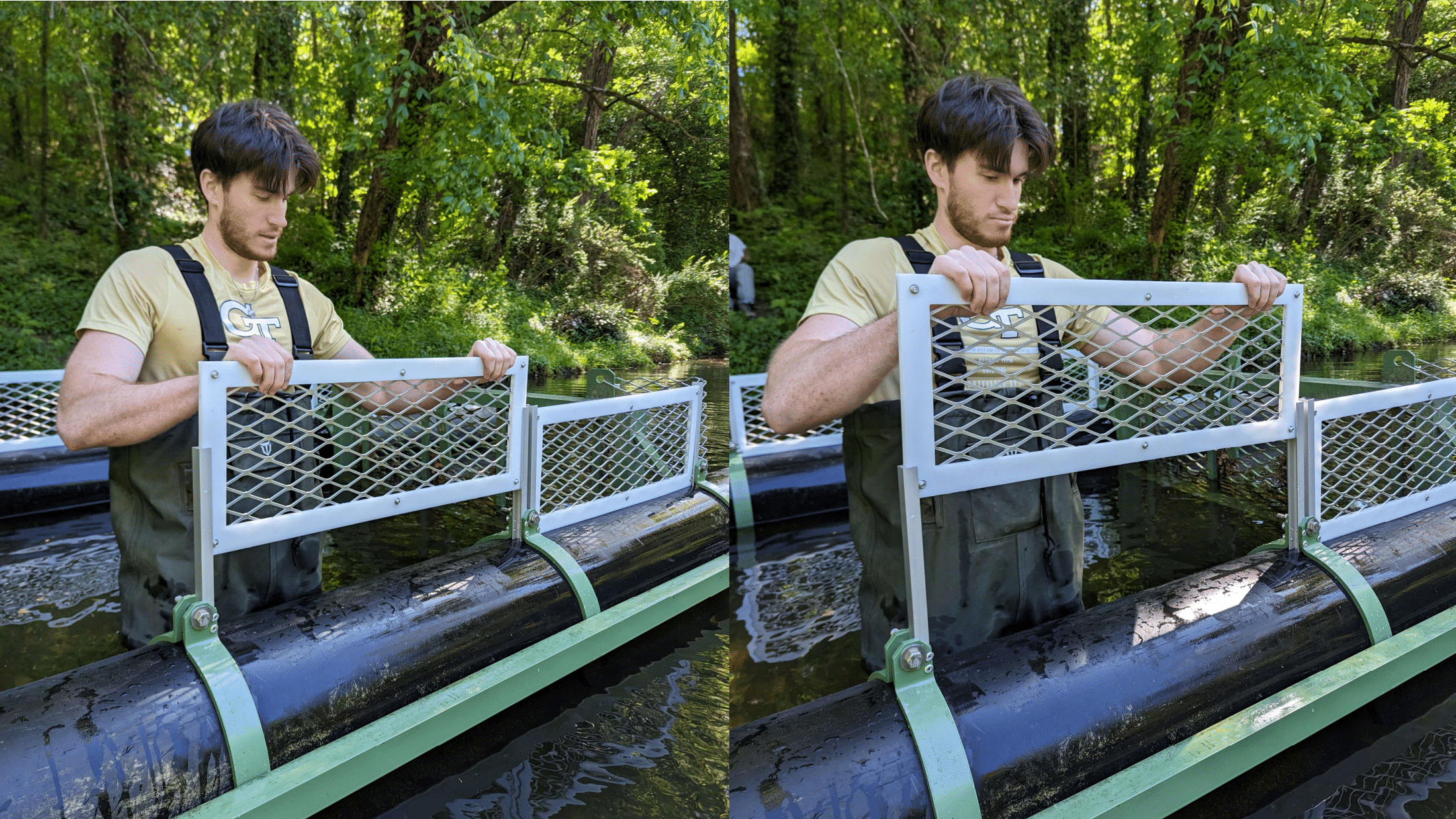

Fabrication Package and Educational Model
All Solidworks and STL files were provided.
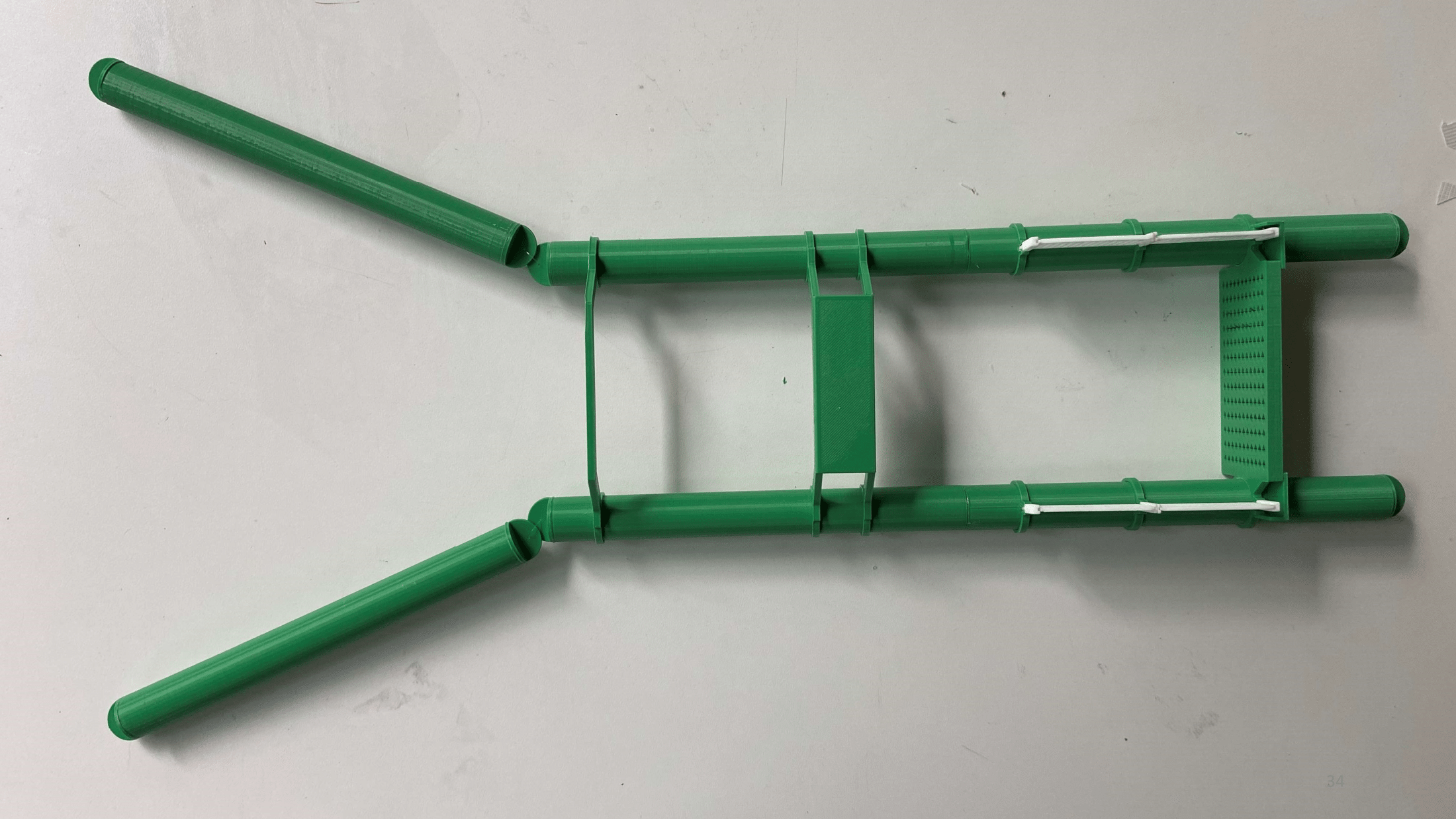
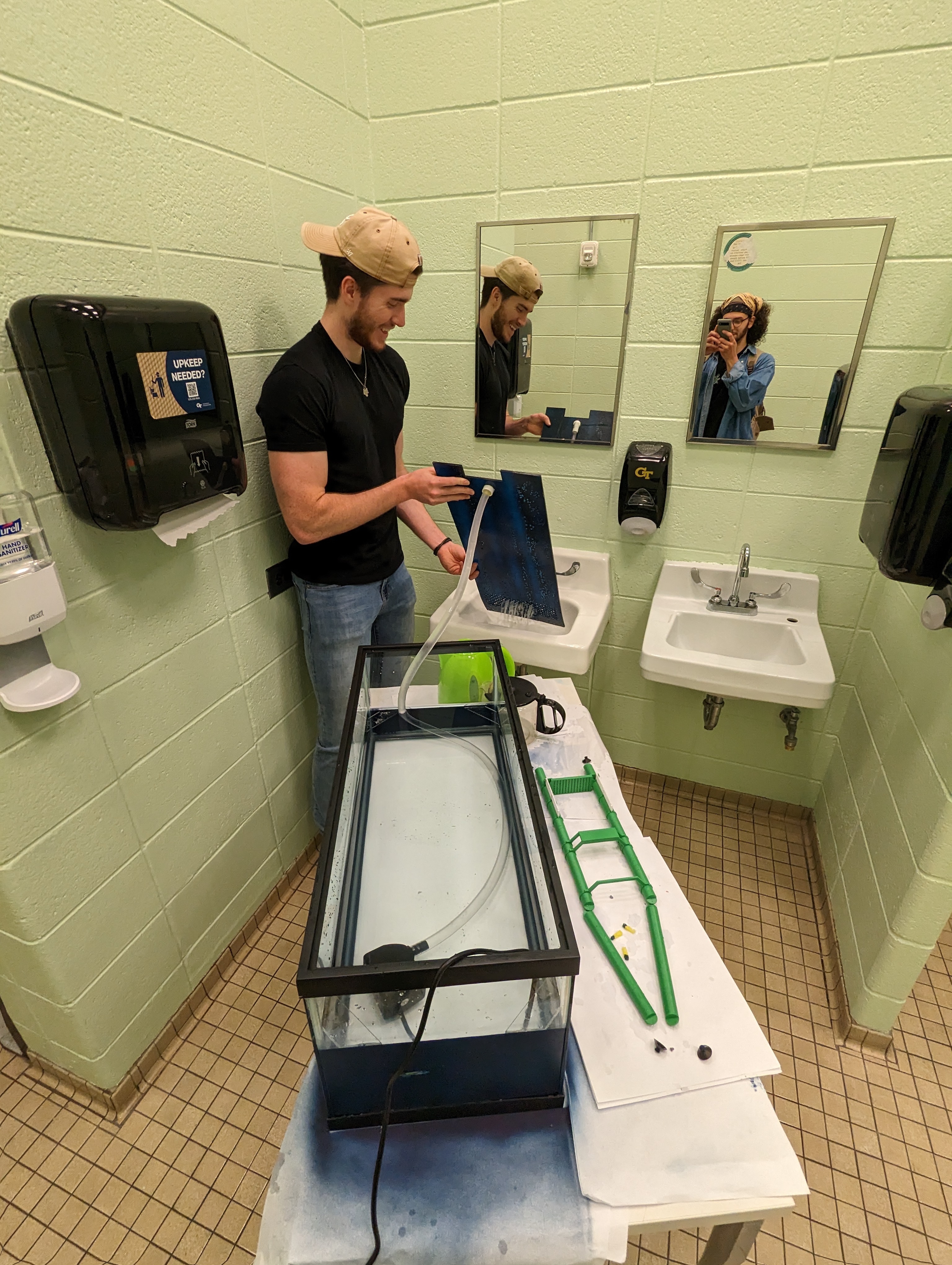
Set up of the educational model. The model consists of a tank with two sections that are seperated by an acrylic sheet. The bottom contains a water pump that simulates the creek flow. On top of the acryllic sheet, the 3d printed model floats and cut up sponges represent the trash.
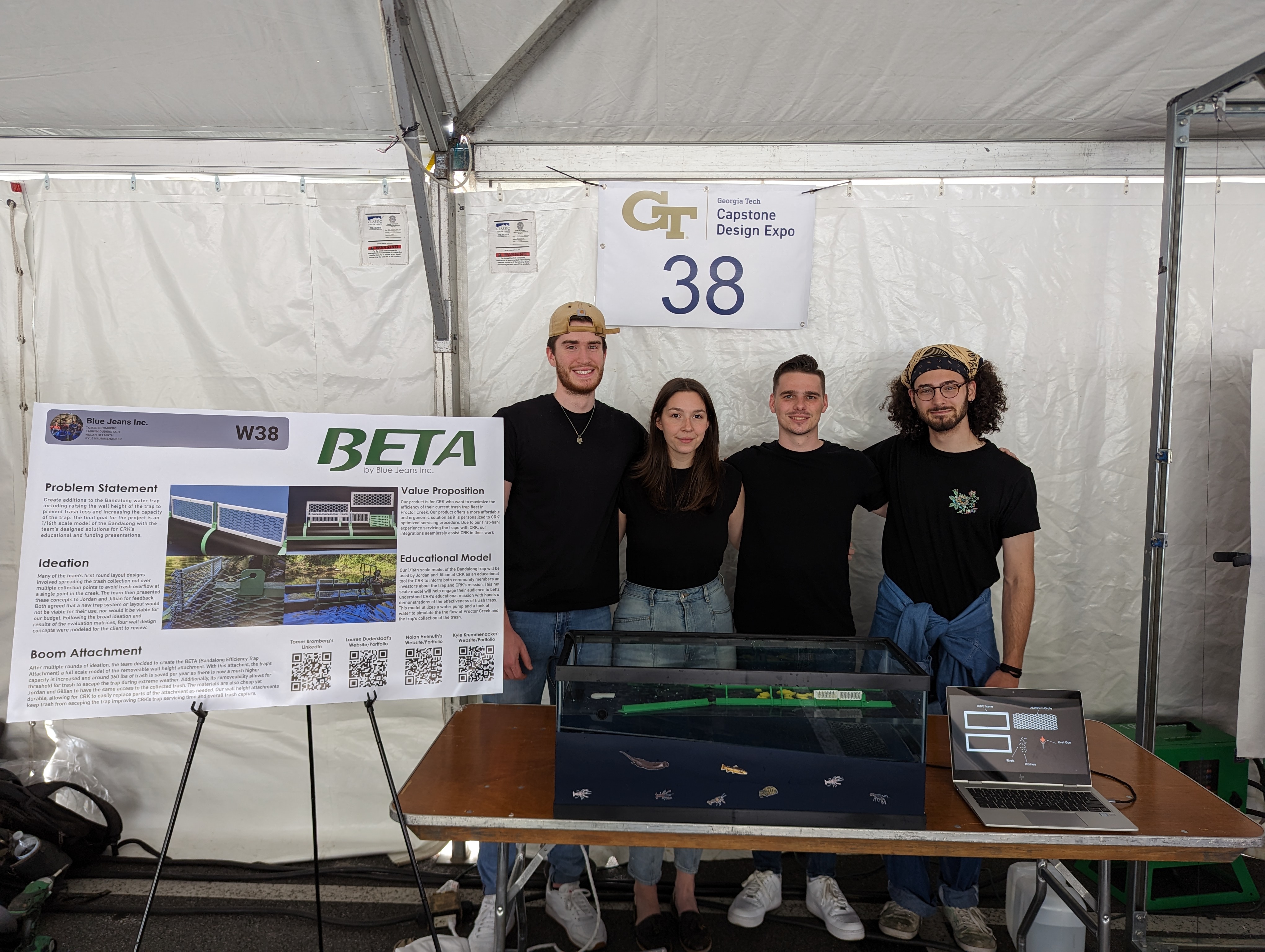
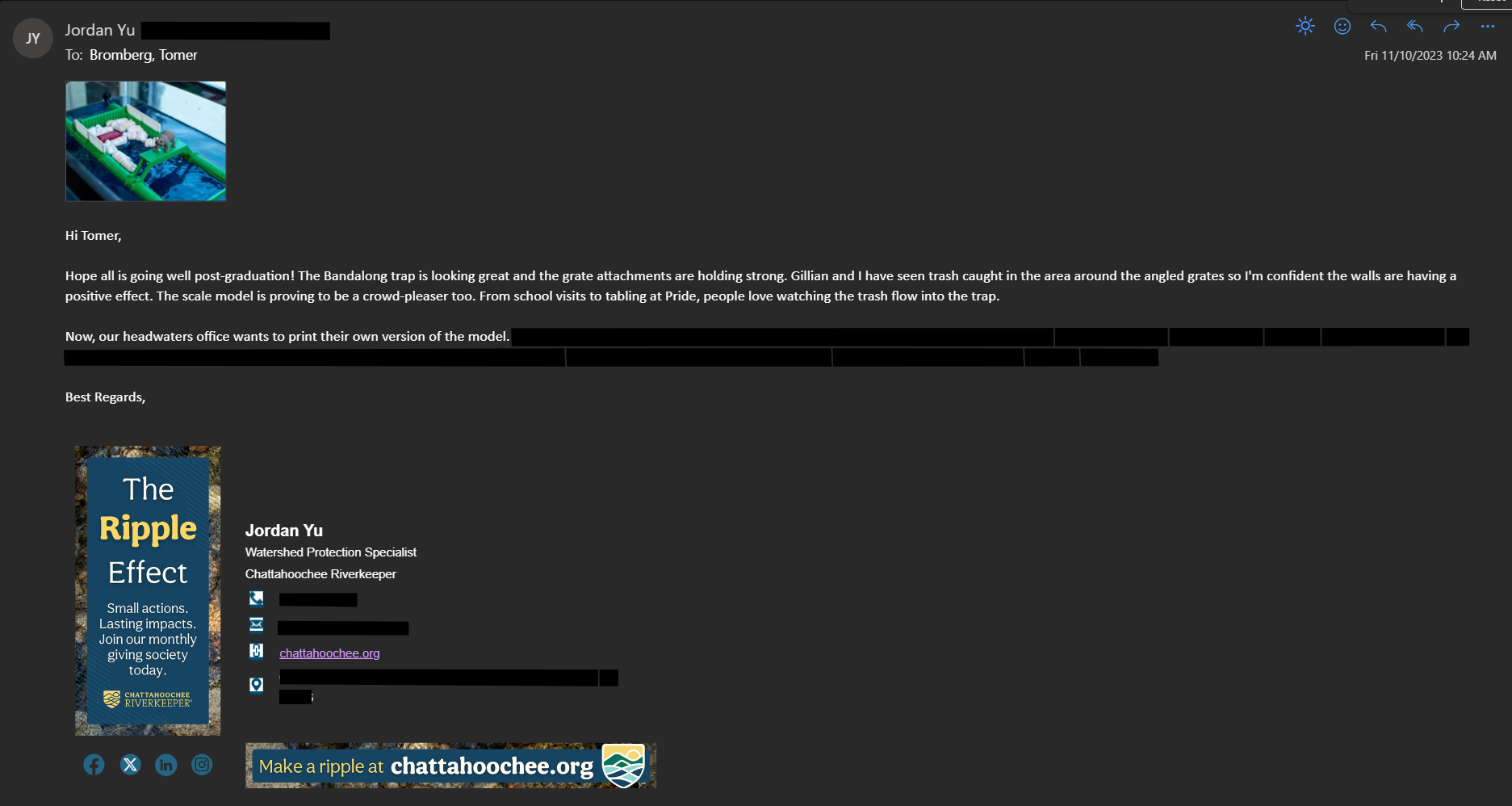
Want more details? Click here to see the entire process.